Color Anodize/Hardcoat
Color Anodize/Hardcoat
APPLICABLE SPECIFICATIONS
MIL-PRF-8625F(2) Type II and III, Class I or II
Colors: Black, Red, Orange, Blue, Gold, Green, Grey
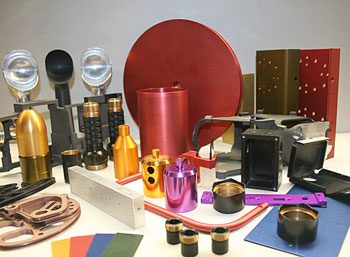
What is it?
Clear anodizing or color anodizing (also known as sulfuric acid anodizing) produces a nearly clear oxide coating which is usually less than 0.0010″ thick. The coating is normally sealed to improve corrosion protection or color-fastness when dyed. Clear anodize (or color anodize) also provide good corrosion protection in mild environments and minimum wear protection.
What does it do?
Sulfuric acid anodizing can provide comparable corrosion resistance and better wear characteristics than chromic acid anodizing. This type of anodizing is used in many architectural applications including windows and door frames, siding, decorative panels, railings, light poles and automotive trim. The coating is frequently colored for decorative purposes using organic dyes or metallic salts. Because of its low cost, this coating is commonly specified on many engineered aluminum components requiring protection from minimum wear and corrosion.
Hardcoat Anodize
APPLICABLE SPECIFICATIONS
MIL-PRF-8625F(2) Type III, Class I or II
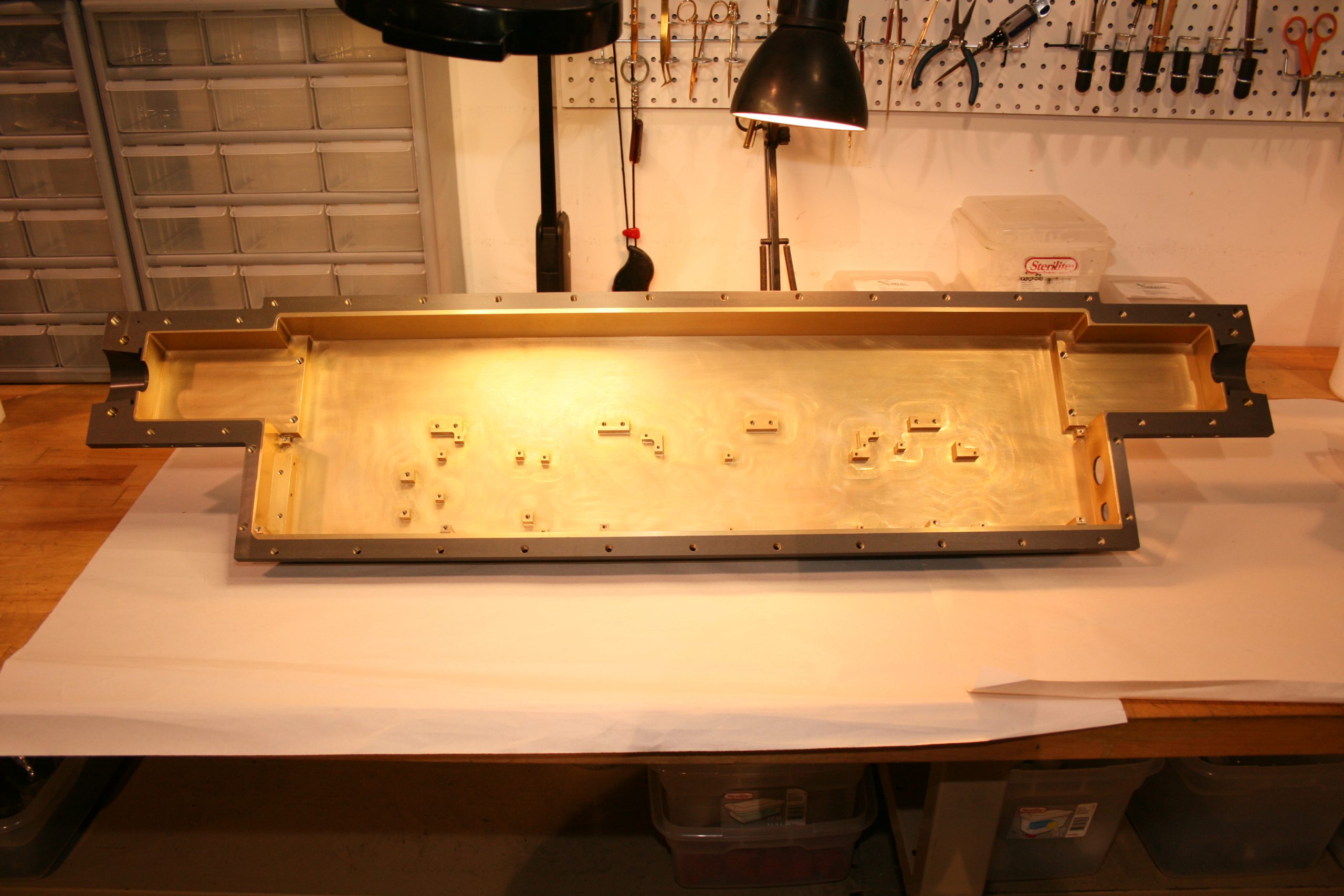
What is it?
Hard Anodizing or Hardcoat Anodize produces an oxide coating that is denser and thicker than sulfuric acid anodize (clear anodize). Film thickness is 3 to 20 times that of chromic or sulfuric acid anodizing and because of the film’s density, it produces a hardness of 60 to 65 Rockwell on the C scale. The color of this film varies from light gray to dark olive gray depending on the material’s alloy, temper and coating thickness.
What does it do?
Wear resistance is the most frequent reason for specifying Hardcoat Anodizing. However, because Hardcoat is also highly dielectric, it is often used to insulate assembly components. Corrosion resistance is a third reason for using Hardcoat. At normal film thickness of 0.002″, the coating offers corrosion protection superior to that of other anodic coatings, especially when it is sealed. Hardcoat is usually applied to machined wrought aluminum. Castings present little difficulty, although pressure die castings yield thin and unpredictable results. Among the many applications that have benefited for years from Hardcoat Anodizing are hydraulic and pneumatic components, pistons, screw threads, high speed machine components, aircraft brake and landing gear components and heat sinks. Hardcoat Anodizing costs more than sulfuric acid anodize but is usually less than chromic acid anodize. In comparison to other wear-resistant coatings applied to aluminum, it is generally much more economical.